Malé úspěchy se promítají do něčeho většího
Pravidelně slavíme velké i malé úspěchy, které mají v našich závodech dopad, ať už jde o zlepšení, nebo o nové projekty. Proto je toto vydání zaměřeno na lidi, kteří se starají o to, aby naše každodenní výroba probíhala hladce a abychom trávili stále méně času „hašením požárů“.
Ve Španělsku, Německu, Číně, Mexiku, České republice, USA nebo na Slovensku pracuje den co den nespočet našich kolegů na optimalizaci a zjednodušení našich procesů. Výčet jejich úspěchů je neuvěřitelně rozmanitý: minimalizace opotřebení nástrojů, podpora týmů z jiných závodů, vzrůstající produktivita lisu, zavedení nových komunikačních kanálů mezi odděleními nebo prostě jen dobrá a čistá práce.
Nebýt úsilí těchto lidí, KAMAX jako celek by nikdy nebyl tak úspěšný a naše společnost by před desítkami let beze stopy zanikla. Ve firmě s téměř 4 000 zaměstnanci je prakticky nemožné představit všechny tyto projekty a lidi. Přesto jsme se snažili zařadit reprezentativní výběr úspěšných projektů z různých míst. Některé z nich jsou větší než jiné, ale všechny mají jedno společné: díky nim se společnost KAMAX stala lepší.

Jeden z mnoha úspěchů: repasování nástrojů v Turnově (Česká republika)
Museros (Španělsko)
Věčný nástroj
Zastavení stroje vlivem nástrojů je jedním z nejnepříjemnějších problémů ve výrobě: může rychle způsobit další komplikace, a proto je potřeba ho neprodleně řešit. Příkladem může být situace, která před několika měsíci nastala ve španělském Muserosu. Po 10 000 vyrobených kusech došlo vlivem rozbití ocelového kroužku k zastavení stroje NEDSCHROEF NB515-1. Bylo třeba najít řešení z hlediska kvality, protože z důvodu problémů se šponkami materiálu v oblasti průměru integrované podložky docházelo ve vysoké míře k vyřazování dílů.
„Mým úkolem bylo zjistit více o problematice materiálu a překážkách, kterým jsme na stroji čelili.“
José „Pepe“ Puchau
Antonio Díaz z výroby, Diego Rodriguez a José Puchau z technologie a Marino Ramos z kvality byli pověřeni vyřešením problému ve spolupráci s operátorem u stroje. „Mým úkolem bylo zjistit více o problematice materiálu a překážkách, kterým jsme na stroji čelili. Díky hlubšímu pohledu a analýze situace našel tým správné řešení,“ uvedl José „Pepe“ Puchau.

Problém úspěšně vyřešen: tým složený z různých oddělení společnosti Museros
Řešením byla výměna ocelového kroužku, který praskal po každých 10 000 vyrobených kusech. Tým vyvinul tvrdokovovou matrici s integrovaným tvarem kroužku. Vzhledem k vysoké odolnosti matrice přišel Antonio s nápadem nazvat ji „věčný nástroj“, jehož životnost se znásobila 35krát. Všichni doufají, že se jim životnost podaří ještě zvýšit.
José „Pepe“ Puchau dodává: „Na týmu mě nejvíce zaujala jeho motivace, touha dělat nové věci a zlepšovat se. Když lidé pracují na správném cíli, vydávají ze sebe to nejlepší, tehdy se nám daří úžasné věci. Zapojení operátorů a techniků, učení se od nich a pomoc lidem k tomu, aby se jim práce líbila, to je to, co mě motivuje.“
Homberg (Německo)
Automatická prioritizace drátů

Mluvčí týmu Andreas Fey určuje priority dodávek drátů
Před lisováním na stroji musí drát obvykle projít dvěma procesními kroky. Musí být předem upraven, aby se zajistilo odstranění všech nečistot a nežádoucích látek, a poté musí být naneseno mazivo. Pokud nemá požadovaný průměr, zahrnuje další krok protažení oceli na tažné stolici. Teprve po dokončení těchto kroků přichází na řadu tváření za studena.
Až donedávna musel mluvčí týmu tažírny v závodě Homberg (Německo) každé ráno v rámci pracovního kokpitu v SAPu zjišťovat, jaký drát je ten den naléhavě potřeba pro lisovnu a tažírnu. Poté v „seznamu pro vychystávání“ stanovil priority drátu, aby systém pro zpracování materiálu v předcházejícím stupni výroby věděl, který materiál má být zpracován jako první. Každý den bylo třeba věnovat procesu prioritizace drátu přibližně tři hodiny – čas strávený plánováním, telefonováním a posíláním e-mailů. Kromě toho tento úkol vázal kapacity jinde, což zase zdržovalo provádění dalších operací.
Ve spolupráci s týmem Nexineer byl vytvořen proces v rámci SAPu, který porovnává data z pracovního kokpitu s materiálem na skladě a automaticky určuje priority potřebných zakázek. Díky tomu může software převzít nudnou část práce – a lidé tak mají více času na své hlavní povinnosti v příslušných odděleních.
Jintan (Čína)
Buddy systém napříč závody
Nový závod Jintan (Čína) je v provozu od třetího čtvrtletí loňského roku, což všichni zaměstnanci obou čínských závodů přijali s velkým nadšením. Při zahájení výroby narazil tým na problémy, jako jsou náročné zákaznické audity či omezené zdroje talentů. Z posledně jmenovaného vyplynula největší výzva pro nový závod – nedostatek kvalifikovaných operátorů a techniků, zejména pro tváření za studena a válcování závitů. Proto byl zaveden buddy systém (systém parťáků/ kamarádů) napříč závody. Ten se osvědčil a je prvním krokem k úspěchu.
Buddy systém znamená vzájemnou podporu mezi našimi dvěma závody. V této konkrétní fázi se jedná především o podporu náběhu v Jintanu, zaměřenou na školení dovedností pro zaměstnance na lisovně a obrobně. Dvouměsíční mentoringový projekt byl zahájen v říjnu. YANG Jinlong byl jedním z nově přijatých operátorů vyslaných do Wujinu. Yangovým školitelem byl jmenován ZHANG Yi, který má více než šestiletou praxi na lisovně. Přibližně po měsíci dorazila druhá dvojice buddíků: YU Xiaosuo, operátor TR z Jintanu, a školitel WANG Youwei z Wujinu. Školitelé vždy postupují podle pokynů pro čtyřstupňové školení nových operátorů:
- Já pracuji, ty se díváš.
- Pracuj se mnou.
- Ty pracuješ, já se dívám.
- Následná kontrola a případná oprava.
Proces tváření za studena a stroje společnosti KAMAX jsou pro tyto zaměstnance něčím zcela novým. Výukové kurzy se týkaly všeho od studia technických výkresů po měření kvality, výměnu razníků, seřizování upínacích prvků, běžné nastavování stroje a řešení problémů. Vzhledem k velké poptávce zákazníků byl čas na zaškolení na stroji omezený, takže záleželo na každé minutě. Společné úsilí obou závodů umožnilo zvýšit produktivitu v Jintanu.
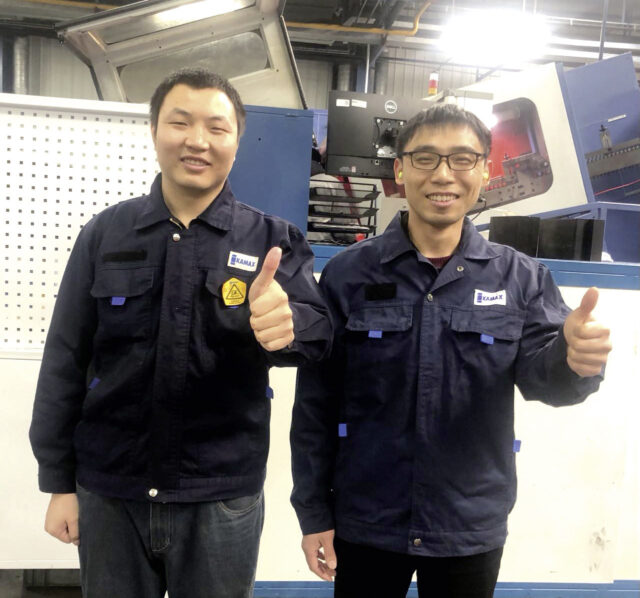
Buddíci z Wujinu a Jintanu: WANG Youwei a Zhang Yi
„Díky úspěchu buddy systému napříč závody plánujeme, že se stane rutinním programem, který bude pokrývat různé úseky.“
JANG Li-pching (Laraine), manažerka lidských ZDROJŮ
Bardejov (Slovensko)
Bardejov podporuje Německo
Na konci loňského roku byl náš závod v Bardejově (Slovensko) požádán, aby podpořil výrobu v Osterode (Německo) tím, že převezme lisování a tepelné zpracování spojovacího materiálu pro společnosti Scania a Daimler. Cílem bylo uvolnit kapacitu strojů OP-OHA.
Vzhledem k odlišnému uspořádání v Bardejově přišel ústřední konstrukční tým s nápadem sestavit sadu nástrojů z modulárního „teleskopického“ designu v Bardejově a klasických konstrukcí z Osterode. Cílem bylo urychlit proces, zkrátit dobu výroby a vyhnout se nedořešeným problémům s modulární konstrukcí. Kolegové z oddělení konstrukce, jak centrální, tak místní, spolupracovali s kolegy z technologie Bardějov a Osterode. Výsledkem bylo úspěšné lisování spojovacích prvků pro společnost Daimler během vánočních svátků. Dodali jsme požadované množství v požadované kvalitě.
Ve stejném týdnu jsme zkusili lisovat spojovací prvky pro společnost Scania, abychom vyzkoušeli nástroje, a uspěli jsme. Bohužel se sada nástrojů velmi brzy rozbila kvůli vadě materiálu. Protože jsme při testu úspěšně dosáhli požadovaných parametrů navzdory prasklině v sadě nástrojů, začali jsme s objednávkou náhrady za poškozený díl. V šestém týdnu tohoto roku, po dodání náhradního dílu, tým úspěšně nalisoval více než 6 000 spojovacích prvků na této sestavě. Ta je připravena k dalšímu lisování. V historii tohoto konkrétního spojovacího prvku se nepodařilo vyrobit více než 3 000 spojovacích prvků bez poškození předchozí sady nástrojů.
Lapeer (USA)
15 minut denně
V Lapeeru se někteří kolegové učí praxi Kata* a experimentují s ní krok za krokem již téměř dva roky – s velkým úspěchem.
„Je to ta nejzábavnější část mého dne,“ řekl Chris Case, zkušený účastník výuky a expert na zlepšování ve výrobě. „Teď nevím, jak toho dosáhnout, ale znám způsob, jak se k tomu dostat,“ říká ke Kata koučinku Mike Freeman, zkušený kouč.
Kata je každodenní praxe, návyk, rutina, kdy kouč a účastník výuky každý den 15 minut provádějí koučovací cyklus podle standardní sady pěti otázek, aby se dopracovali k úspěchu. Praxe Kata spočívá v rozvoji kultury vědeckého myšlení tím, že si každý den záměrně zapíšeme další krok a to, co od něj očekáváme, a následující den zhodnotíme, co se během tohoto kroku stalo a co jsme se naučili. Neztrácíme čas hádáním řešení, ale zaměřujeme se na metodiku „Jdi a dívej se“, kdy nejprve do hloubky porozumíme svému současnému stavu a poté se denně krok za krokem pohybujeme nejistotou, abychom dosáhli toho, čeho potřebujeme dosáhnout.
„V současné době s pomocí Jona Sharpa a oddělení OPEX zavádíme Kata koučink i v dalších závodech. Pokračujeme v procesu zapracování našich kolegů v Evropě a Číně a pracujeme také virtuálně z Lapeeru,“ říká Ron Darling, výrobní inženýr v Lapeeru.
* Termín kata pochází z japonských bojových umění a označuje podrobnou definici pohybových sekvencí. Ty se díky praxi a aplikaci stávají natolik rutinními a zvnitřněnými, že je provádíme téměř reflexivně, bez přemýšlení.
Turnov (Česká republica)
Recyklace místo nákupu
Nejziskovějším závodem skupiny je KAMAX v Turnově (Česká republika). Ani zde nejsou úspěchem pouze velké projekty a milníky. Často se jedná o kombinovaný efekt několika drobných zlepšení a optimalizací. Dobrým příkladem je proces pro použité nástroje.
Namísto nahrazování použitých nástrojů novými tým v Turnově nejprve posoudí všechny nástroje, které již byly ve strojích použity, aby získal přehled o tom, které z nich by mohly být vhodné pro opravu a opětovné použití. Méně poškozené díly se pak na základě výkresů a dokumentace porovnávají s objednávkovým seznamem nových nástrojů. Pokud jsou použité nástroje vhodné, jsou opraveny a upraveny a po následné kontrole označeny jako „REPAS“.
Namísto nových nástrojů se pak znovu nasazují do strojů. Teprve když užitečnost opravených nástrojů klesne pod určitou mez, jsou z procesu vyřazeny. Za poslední rok se týmu podařilo díky recyklaci „šrotu“ ušetřit více než 50 000 eur, a to i po odečtení nákladů na opravy.
Těchto šest projektů je samozřejmě jen malým vzorkem ze světa KAMAX, ale jasně ukazují jednu věc: malé úspěchy se promítají do něčeho většího. A jen pokud zůstaneme zapálení pro věc, budeme se i nadále snažit odstraňovat drobné chyby v naší každodenní práci, měnit procesy tak, aby nám usnadňovaly práci, a navzájem si pomáhat svými znalostmi a zkušenostmi, zůstaneme úspěšnou firmou.
KXpress