Kleine Erfolge machen uns groß
In unseren Werken feiern wir regelmäßig kleine und große Erfolge, mit Verbesserungen und neuen Projekten, die Wirkung zeigen. Deshalb stellen wir in dieser Ausgabe die Menschen in den Mittelpunkt, die dafür sorgen, dass unser Produktionsalltag rund läuft und wir immer weniger Brände löschen müssen.
Ob in Spanien, Deutschland, China, Mexiko, Tschechien, den USA oder der Slowakei: Unzählige Kolleginnen und Kollegen arbeiten täglich daran, Prozesse zu optimieren und zu vereinfachen. Dabei geht es um die unterschiedlichsten Dinge: Werkzeugverschleiß minimieren, Teams aus anderen Werken unterstützen, die Produktivität einer Presse steigern, neue Kommunikationswege zwischen Abteilungen etablieren oder einfach nur einen sauberen und guten Job machen.
Ohne den Einsatz dieser Menschen wäre KAMAX als Gesamtunternehmen nie erfolgreich gewesen und schon vor Jahrzehnten in der Versenkung verschwunden. Wirklich alle Projekte und Menschen abzubilden, ist bei fast 4.000 Mitarbeitenden nahezu unmöglich. Dennoch haben wir uns auf die Suche gemacht, um zumindest einige Erfolgsgeschichten aus den verschiedenen Standorten zu erzählen. Manche sind größer, manche kleiner, aber eines haben alle gemeinsam: Sie machen KAMAX besser.

Ein kleiner Schritt von vielen: Wiederaufbereitung der Werkzeuge in Turnov (Tschechien)
Museros (Spanien)
Das ewige Werkzeug
Ein Maschinenausfall ist eines der ärgerlichsten Probleme in der Produktion. Er kann in kürzester Zeit zu weiteren Komplikationen führen und muss schnell behoben werden. Das war in Museros (Spanien) vor einigen Monaten der Fall. Ein Bruchproblem verursachte den Stillstand der NEDSCHROEF NB515-1 nach einem Satz von 10.000 gefertigten Teilen. Eine hohe Anzahl von Teilen wurde aufgrund von Materialklumpen im Flanschdurchmesser zurückgewiesen. Es musste eine Lösung gefunden werden.
„Ich habe mir die Materialprobleme und Hindernisse angeschaut, mit denen wir an der Maschine konfrontiert waren.“
José „Pepe“ Puchau
Gemeinsam mit den Maschinenbedienern sollten Antonio Díaz (Produktion), Diego Rodriguez (TECH), Marino Ramos (QM) und José Puchau (TECH) das Problem lösen. „Ich habe mir die Materialprobleme und Hindernisse angeschaut, mit denen wir an der Maschine konfrontiert waren. Das genaue Hinschauen und Analysieren half dem Team die richtige Lösung zu finden“, sagt José „Pepe“ Puchau.

Hat das Problem erfolgreich behoben: das abteilungsübergreifende Team von Museros
Das Team ersetzte die brüchige Stahlplatte durch eine selbstentwickelte Hartmetallmatrix in der integrierten Form der Platte. Die hohe Haltbarkeit der Platte bescherte ihr auch den Namen „ewiges Werkzeug“, eine Idee von Antonio. Die Maschinenlaufzeit stieg durch das neue Werkzeug um das 35-fache und soll weiter erhöht werden.
Puchau fasst zusammen: „Was mich am meisten an der Teamzusammenarbeit beeindruckt hat, war die Motivation und der Wunsch, neue Dinge zu tun und sich zu verbessern. Mit dem richtigen Ziel holen die Menschen das Beste aus sich heraus, und dann leisten wir Großartiges. Die Einbeziehung von Bedienern und Technikern, das Lernen von ihnen und das Ziel, dass die Leute ihre Arbeit mögen, motiviert mich immer wieder.“
Homberg (Deutschland)
Automatische Priorisierung des Drahts

Teamsprecher Andreas Fey priorisiert die Drahtlieferungen
Bevor der Draht auf unseren Maschinen gepresst wird, durchläuft er zuvor meist noch zwei weitere Prozessschritte: Er wird in der WBA vorbehandelt, um alle Störfaktoren auf dem Material zu beseitigen und mit einem Schmiermittel versehen. Falls der Durchmesser noch abweicht, wird der Stahl im nächsten Schritt in der Zieherei so gedehnt, dass alles haargenau stimmt. Erst danach geht es in die Kaltumformung.
Im Homberger Werk (Deutschland) hat bis vor Kurzem der Teamsprecher der Zieherei jeden Morgen im sog. Werkercockpit in SAP geprüft, welcher Draht an diesem Tag für die Presserei und die Zieherei (dringend) benötigt wird. In einer „Picklist“ priorisierte er dann den Draht, sodass die vorgelagerte WBA wusste, welchen Werkstoff sie zuerst behandeln musste. Für die Priorisierung des Drahtes fielen pro Tag ca. drei Stunden für Planung inkl. Telefonate und Mails an. Kurzfristige Ausfälle konnten nur schwer kompensiert werden. Zudem war durch diese Aufgabe die Kapazität an anderer Stelle gebunden, was wiederum für Verzögerung bei der Ausführung weiterer Aufgaben sorgte.
Gemeinsam mit dem Team der Nexineer wurde hier innerhalb von SAP ein Prozess entwickelt, der die Daten aus dem Werkercockpit mit dem vorhandenen Werkstoff vergleicht und automatisch die notwendigen Aufträge priorisiert. Damit übernimmt die Software den mühseligen Teil der Arbeit, sodass mehr Zeit für die Hauptaufgaben in den jeweiligen Abteilungen bleibt.
Jintan (China)
Werksübergreifendes Buddy-System
Seit Oktober 2022 ist neben Wujin auch das neue Werk in Jintan (China) in Betrieb. Alle Mitarbeitenden waren sehr aufgeregt. Mit dem Beginn des Baus und der Fertigung sah sich das Team mit verschiedenen Herausforderungen konfrontiert, wie z. B. intensiven Kundenaudits und Fachkräftemangel aufgrund der lokalen Industriestruktur. Letzteres stellte die größte Hürde für das neue Werk dar – insbesondere für das Kaltstauchen und Gewindewalzen herrschte ein Mangel an qualifizierten Bedienern und Technikern. Daraus entstand die Idee eines werksübergreifenden Buddy-Systems – der erste Schritt zum Erfolg.
Das werksübergreifende Buddy-System lebt von der gegenseitigen Unterstützung zwischen unseren beiden chinesischen Werken. In dieser besonderen Zeit hilft das Projekt vor allem in der Anlaufphase in Jintan, mit dem Schwerpunkt Kaltstauchen und Gewindewalzen Mitarbeitende auszubilden. Das zweimonatige Mentoring-Projekt begann im Oktober. YANG Jinlong war einer der ersten Teilnehmer, die nach Wujin geschickt wurden. ZHANG Yi, der mehr als sechs Jahre Erfahrung in der Kaltumformung sammeln konnte, wurde YANGs Tutor. Einen Monat später fand sich das zweite Team mit YU Xiaosuo, TR-Operator aus Jintan und WANG Youwei aus Wujin. Das Mentoring-Programm folgt dabei folgenden vier Schritten:
- Ich mache; du schaust zu.
- Wir machen gemeinsam.
- Du machst; ich schaue zu.
- Ich helfe und korrigiere, wenn nötig
Abläufe, Verfahren und Maschinen sind neu für die Kolleg*innen, daher umfassen die Schulungen den gesamten Prozess von Zeichnungserkennung bis zur Qualitätsmessung, vom Wechsel der Matrize/Stempel bis zur Einstellung der Vorrichtungen und von der normalen Feineinstellung der Maschine bis zur Fehlerbehebung. Aufgrund der großen Kundennachfrage stand nur eine begrenzte Zeit für die Schulung an der Maschine zur Verfügung, so dass jede Minute zählte. Die gemeinsamen Anstrengungen beider Werke haben es ermöglicht, die Produktivität in Jintan in kürzester Zeit zu verbessern.
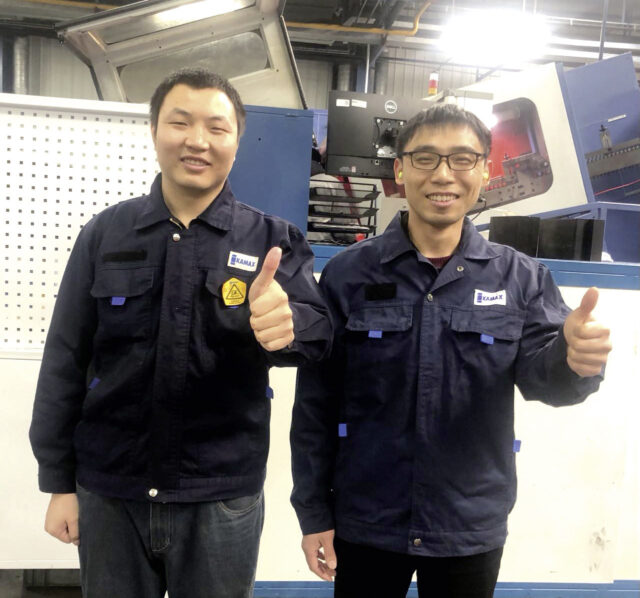
Das Tutorenteam aus Wujin: WANG Youwei (links) und Zhang Yi (rechts)
„Nach dem ersten Erfolg dieses werksübergreifenden Buddy-Systems planen wir ein Routineprogramm. Wir werden verschiedene Bereiche zwischen den zwei Werken vernetzen, um die Stärken der verschiedenen Teams zu maximieren!“
YANG Liping (Laraine),
P&C Managerin
Bardejov (Slowakei)
Bardejov unterstützt Osterode
Ende letzten Jahres halfen unsere Kolleg*innen in Bardejov (Slowakei) bei der Produktion von Schrauben für Scania und Daimler aus. Damit sollten Kapazitätsengpässe auf den Maschinen in Osterode behoben werden.
Die Herausforderung war, verschiedene Systeme zusammenzubringen, um die Produkte herzustellen. Daher kam das zentrale Konstruktionsteam auf die Idee, den Werkzeugsatz aus einer Mischung der modularen „Teleskopmatrizen“ in Bardejov und den klassischen Konstruktionen aus Osterode zusammenzustellen. Ziel war es, den Prozess zu beschleunigen, die Produktionszeit zu verkürzen und ungelöste Probleme mit dem modularen Aufbau zu vermeiden. Kolleg*innen aus der zentralen und lokalen Konstruktionsabteilung arbeiteten mit den Teams von TEC BAR und TEC OHA zusammen. So war es uns möglich, zwischen den Weihnachtsfeiertagen erfolgreich Verbindungselemente für Daimler zu pressen: Wir lieferten die benötigte Menge in der erforderlichen Qualität.
In der gleichen Woche pressten wir die Verbindungselemente für Scania. Leider brach jedoch der Werkzeugsatz aufgrund von Materialfehlern sehr früh. Da der Test trotzdem die geforderten Parameter erreichte, begannen wir mit der Bestellung eines Ersatzes für das beschädigte Teil. Nachdem das Ersatzteil geliefert worden war, produzierte das Team mehr als 6.000 Schrauben an dieser Baugruppe. Und wir sind bereit für weitere Verpressungen.
Lapeer (USA)
15 Minuten pro Tag
In Lapeer haben Kolleg*innen in den letzten zwei Jahren schrittweise die Kata*-Praxis erprobt und gelernt – mit Erfolg.
„Es ist der Teil meines Tages, der am meisten Spaß macht“, sagt Chris Case, ein erfahrener Kata Anwender in der Produktion. „Ich weiß nicht, wie ich mein Ziel erreichen kann, aber ich kenne einen Weg dorthin“, sagt Mike Freeman, Kata-Trainer und Lernender in der Technik.
Kata ist eine tägliche Praxis, eine Routine, bei der ein Coach und ein Lernender täglich 15 Minuten lang einen Coaching-Zyklus durchführen und fünf Fragen folgen, um auf ein Ziel hinzuarbeiten. Bei der Kata-Praxis geht es darum, eine Analyse-Kultur zu entwickeln, indem wir jeden Tag absichtlich unseren nächsten Schritt aufschreiben, was wir von diesem Schritt erwarten und dann am nächsten Tag überprüfen, was während dieses Schritts passiert ist und was wir gelernt haben. Wir verbringen keine Zeit damit, Lösungen zu erraten, sondern konzentrieren uns auf eine „Go and See”-Methode, bei der wir den Ist-Zustand verstehen und Schritt für Schritt in Richtung Ziel gehen.
„Den Aufbau von Kata-Coaches wollen wir auch auf andere Standorte ausrollen – mit Hilfe von Jon Sharp und OPEX. Dazu soll ein Onboarding-Prozess mit Kolleg*innen in Europa und China durchgeführt werden“, sagt Ron Darling, Fertigungsingenieur in Lapeer.
* Der Begriff Kata stammt aus dem japanischen Kampfsport und bezeichnet die detaillierte Beschreibung von Bewegungsabläufen. Diese werden durch Übung so routiniert und verinnerlicht, dass sie fast reflexartig ohne Nachdenken ausgeführt werden.
Turnov (Tschechien)
Recycling statt Neukauf
Mit Blick auf die letzten Jahre ist Turnov (Tschechien) das profitabelste Werk der KAMAX Gruppe. Aber auch hier sind es nicht immer die großen Projekte und Meilensteine, sondern oft die Summe der kleinen Verbesserungen und Optimierungen, die den Standort erfolgreich machen. Nur ein Beispiel ist der Umgang mit gebrauchten Werkzeugen.
Anstatt benutzte durch neue zu ersetzen, sortiert das Team von Václav Šantin in Turnov zuerst alle Werkzeuge, die bereits in Maschinen eingesetzt wurden, um sich einen Überblick zu verschaffen, welche eventuell repariert und wiederverwendet werden können. Das Team vergleicht dann die weniger stark beschädigten Teile aus dem „Schrott“ anhand der Zeichnungsunterlagen mit der Auftragsliste für neue Werkzeuge. Wenn ein gebrauchtes Werkzeug passt, wird es repariert und angepasst und nach anschließender Prüfung mit „REWORKED“ markiert.
Diese „REWORK“-Werkzeuge werden priorisiert und im Einsatz an den Maschinen neuen Bestellungen vorgezogen. Erst wenn die Haltbarkeit des reparierten Tools eine bestimmte Grenze unterschreitet, wird es aus dem Prozess entfernt. Im vergangenen Jahr gelang es Václavs Team mit diesem Vorgehen über 50.000 Euro einzusparen, indem sie „Schrott“ recycelten – die Kosten der Reparatur miteingerechnet.
Diese sechs Projekte sind sicherlich nur ein kleiner Ausschnitt aus der KAMAX Welt, aber sie zeigen eins ganz deutlich: Der kleine Erfolg macht uns als Unternehmen groß! Und nur wenn wir so hungrig bleiben, die kleinen Fehler im Alltag ausmerzen, Prozesse so ändern, dass sie uns die Arbeit erleichtern und uns gegenseitig mit Wissen und Erfahrung unterstützen, schaffen wir es, ein erfolgreiches Unternehmen zu bleiben.
KXpress