Little successes translate into something bigger
We regularly celebrate successes both large and small that are having an impact in our plants, be it improvements or new projects. That is why this issue is focused on the people who ensure that our day-to-day production runs smoothly and that we spend less and less time “putting out fires.”
Be it in Spain, Germany, China, Mexico, the Czech Republic, the USA, or Slovakia, untold numbers of our colleagues are working day in and day out to optimize and simplify our processes. Their accomplishments are incredibly diverse: minimizing tool wear, supporting teams from other plants, increasing the productivity of a press, establishing new communication channels between departments, or simply doing a good, clean job.
Were it not for the efforts of these people, KAMAX as a whole would never have been such a success, and our company would have disappeared without a trace decades ago. In a firm with nearly 4,000 employees, it would be practically impossible to feature every single one of these projects and people. Even so, we did our best to include a representative selection of success stories from various locations. Some of them are bigger than others, but they all have one thing in common: they have made KAMAX better.

One small step of many worldwide: reprocessing of tools in Turnov (Czech Republic)
Museros (Spain)
The forever tool
Machine breakdown is one of the most annoying problems in production; it can quickly cause further complications and must be solved without delay. An example of this occurred at Museros (Spain) a few months ago. A breakage problem caused a stoppage of the NEDSCHROEF NB515-1 after a set of 10,000 manufactured parts. A solution needed to be found from a quality perspective, as there was a high rejection of parts due to problems involving material lumps in the flange diameter.
“My task was to learn more about the material issues and the obstacles we faced in the machine.”
José “Pepe” Puchau
Antonio Díaz from Production, Diego Rodriguez from TECH, Marino Ramos from QM, and José Puchau from TECH were assigned to work with the machine operators to solve the problem. “My task was to learn more about the material issues and the obstacles we faced in the machine. By having a deeper look and analyzing the situation, the team found the right solution,” said José “Pepe” Puchau.

Has successfully fixed the problem: the cross-departmental team from Museros
The solution was to replace the steel plate, which was breaking after every 10,000 parts. The team developed a hard metal matrix with the integrated shape of the plate. Due to the high durability of the plate, Antonio came up with the idea of calling it the “forever tool.” The machine runtime has now been multiplied by 35 with this tool, and they hope to increase it further.
José “Pepe” Puchau: “What has impressed me the most about the team is their motivation and desire to do new things and improve. When people are working towards the right goal, they bring out the best in themselves, and that’s when we do awesome things. Getting operators and technicians involved and learning from them, and helping people to like their work, this is what always motivates me.”
Homberg (Germany)
Automatic prioritization of wire

Team speaker Andreas Fey priotizes the wire deliveries.
Before wire is pressed on our machines, it must normally be put through two additional process steps. The wire must be pre-treated in the material treatment system to ensure that all impurities and unwanted substances are removed, and then lubricant must be applied. In the event that the diameter is still not quite what it should be, the next step involves pulling the steel in the drawing mill to achieve the precise diameter required. Only then, after this has been done, it is time for the cold-forming process.
Until recently, the drawing mill’s team speaker at the Homberg plant (Germany) had to go to the “worker cockpit” in SAP every morning to see which wire was required (urgently) that day for the pressing shop and the drawing mill. They then prioritized the wire in the “pick list” to ensure that the upstream material treatment system would know which material should be processed first. Every day, approx. three hours had to be devoted to the process of prioritizing the wire, time spent on planning, making phone calls, and sending emails. Anytime something shut down at short notice, it was difficult to compensate. In addition, this task tied up capacities elsewhere, which in turn delayed the execution of other operations.
Together with the Nexineer team, they created a process within SAP here that compares data from the “worker cockpit” with the materials on hand and automatically prioritizes the necessary jobs. As a result, the software is able to take on the tedious part of the work – allowing more time for people to take care of their primary responsibilities in their respective departments.
Jintan (China)
The cross-plant buddy system
The new Jintan (China) plant has been in operation since the third quarter of last year, something met with great excitement by all employees in both plants. As they started overall setup and production, the team encountered challenges, such as demanding customer audits and limited talent resources due to the local industry structure. The latter resulted in the biggest challenge for the new plant – a lack of skilled operators and technicians, especially for cold heading and thread rolling. Therefore, a cross-plant buddy system was implemented. This has worked well and is the first step toward success.
The cross-plant buddy system means mutual support between two of our plants. At this particular stage, it refers mainly to support for the ramp-up in Jintan focused on skill training for cold-heading and thread-rolling operators. The two-month mentoring project started in October. YANG Jinlong was one of the newly recruited operators sent to Wujin. ZHANG Yi, who has more than six years of cold-heading experience in Wujin, was appointed YANG’s tutor. After about a month, the second pair of buddies arrived: YU Xiaosuo, TR operator from Jintan, and tutor WANG Youwei from Wujin also started their new journey. The tutors followed the instructions for the four-step training of new operators:
- I do; you watch.
- Do with me.
- You do; I watch.
- Follow up and correct.
KAMAX’s cold-forming process and machines are completely new activities for these employees. The tutorials covered everything from drawing recognition to quality measurement, die/punch changeovers, fixture adjustment, normal machine fine-tuning, and troubleshooting. Due to strong customer demand, there was limited time for training on the machine, so every minute counted. The joint efforts of both plants have made it possible to improve productivity at Jintan.
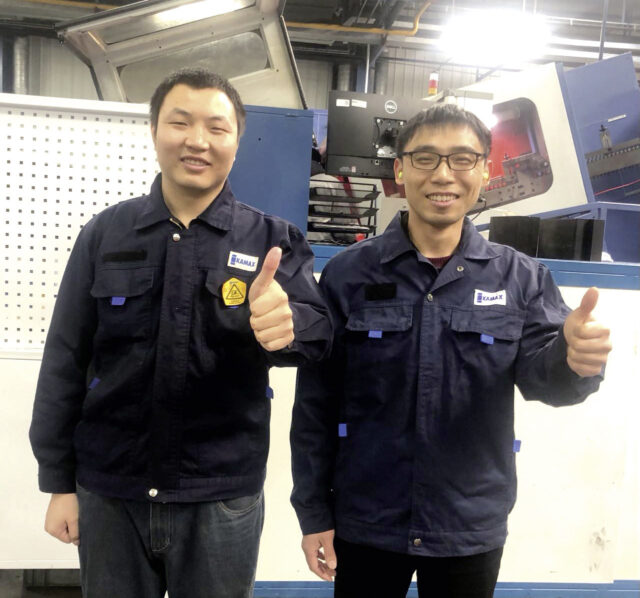
The cross-plant buddies WANG Youwei and Zhang Yi
“Thanks to the success of this cross-plant buddy system, we plan to make it a routine program, covering dif ferent sections between two plants to maximize the advantages of different teams.”
YANG Liping (Laraine), People & Culture Manager
Bardejov (Slovakia)
Bardejov supports Germany
At the end of last year, our plant in Bardejov (Slovakia) was asked to support Osterode (Germany) production by taking over the cold heading and heat treating of fasteners for Scania and Daimler. The goal was to free up capacity on the OP-OHA machines.
Due to the different setup in Bardejov, the central design team came up with the idea of assembling the toolset from the modular “telescopic” design in Bardejov and classic designs from Osterode. The aim was to speed up the process, reduce production time, and avoid unresolved issues with the modular design. Colleagues from the design department, both central and local, worked with colleagues from TEC BAR and TEC OHA. As a result, we successfully pressed fasteners for Daimler during the Christmas holidays. We shipped the required quantity in the required quality.
In the same week, we tried to press the fasteners for Scania as a tool test, which was successful. Unfortunately, the toolset broke very early due to faulty material. As the test successfully achieved the required parameters despite the crack in the toolset, we started ordering a replacement for the damaged part. In the sixth week of this year, after delivering the spare part, the team successfully pressed more than 6,000 fasteners on this assembly. It is ready for further pressing. In the history of this particular fastener, more than 3,000 fasteners could not be ejected without damaging the previous toolset.
Lapeer (USA)
15 minutes a day
In Lapeer, some colleagues have been learning Kata* practice and experimenting with it, step by step, for nearly two years now – with great success.
“It’s the most fun part of my day,” said Chris Case, an experienced
learner, and improver in production. “I don’t know how to achieve that
right now, but I do know a way to get there,” said Mike Freeman, an
experienced Kata coach, and learner in Engineering.
Kata is a daily practice, a habit, a routine where a coach and learner conduct a daily coaching cycle for 15 minutes, every day, following a standard set of five questions to work toward achievement. The Kata practice is all about developing a culture of scientific thinking by intentionally writing down our next step each day, and what we expect from taking that step, and then on the following day reviewing what happened during that step and what we learned. We don’t spend time guessing at solutions, but rather focus on a “Go and See” methodology of first gaining an in-depth understanding of our current condition, and then navigating daily, step by step, through the uncertainty to achieve what we need to achieve next.
“With regard to training Kata coaches, we are currently in the process of rolling out the Kata program at other locations with the assistance of Jon Sharp and OPEX. We are also pursuing the onboarding process with our colleagues in Europe and China, as well as working virtually from Lapeer,” said Ron Darling, Manufacturing Engineer in Lapeer.
* The term kata comes from Japanese martial arts and refers to the detailed definition of movement sequences. These become so routine and internalized through practice and application that they are executed almost reflexively without thinking.
Turnov (Czech Republic)
Recycling instead of purchasing
In recent years, Turnov (Czech Republic) has been the most profitable plant in the KAMAX Group. Yet here too, it is not always the major projects and milestones that make the location a success. Instead, it is often the combined effect of all the little improvements and optimizations. The process for used tools is a good example.
Instead of replacing used tools with new ones, Václav Šantin and his team in Turnov first assess all the tools that have already been used in machines to gain an overview of which ones might actually be suitable for repair and reuse. The team then compares the less-damaged parts from “scrap” based on drawings and documentation with the order list for new tools. If a used tool is suitable, it is then repaired and adapted and – following a subsequent inspection – labeled “REPAS.”
Instead of ordering new tools, these “REPAS” tools are then put back to work in the machines. It is only when the utility of the repaired tools falls below a specific threshold that they are removed from the process. Over the past year, Václav’s team has managed to save over €50,000 through this process by recycling “scrap” – even after the costs of the repairs.
These six projects are clearly no more than a small sample from the KAMAX world, but they show one thing very clearly: little successes translate into something bigger. And it is only if we stay hungry, keep working to eliminate the little errors in our daily work, continue striving to change processes in ways that make our work easier, and help one another with our knowledge and experience, that we will remain a successful company.
KXpress