Pequeños éxitos que se traducen en algo grande
Periódicamente celebramos los éxitos grandes y pequeños que tienen impacto sobre nuestras plantas, ya sean mejoras o nuevos proyectos. Por eso, este número se centra en la gente que garantiza que nuestra producción diaria marche como la seda y que pasemos cada vez menos tiempo “apagando fuegos”.
Tanto en España como en Alemania, China, México, la República Checa, Estados Unidos o Eslovaquia, son innumerables los compañeros que trabajan día tras día optimizando y simplificando nuestros procesos. Sus logros son increíblemente diversos: reducir el desgaste de las herramientas, apoyar a equipos de otras plantas, aumentar la productividad de una prensa, crear nuevos canales de comunicación entre departamentos o simplemente hacer bien el trabajo.
Si no fuera por el esfuerzo de todos estos compañeros, KAMAX, en su conjunto, nunca habría tenido ese éxito y nuestra compañía habría desaparecido sin rastro alguno hace décadas. En una empresa con casi 4.000 empleados sería prácticamente imposible presentar cada uno de esos proyectos y personas. Algunos de ellos son de mayor relevancia que otros, pero todos tienen una cosa en común: han hecho y hacen mejor a KAMAX.

Un pequeño paso de muchos en todo el mundo: reprocesando herramientas en Turnov (República Checa)
Museros (España)
Una herramienta para siempre
Que una máquina se averíe es una de las cosas que más problemas causan en producción, pues una avería puede provocar rápidamente otras complicaciones y debe resolverse sin dilación alguna. Algo así ocurrió en Museros (España) hace unos meses. Una rotura causó la parada de la máquina NEDSCHROEF NB515-1 después de procesar un juego de 10.000 piezas. Se necesitaba encontrar una solución desde una perspectiva de calidad, puesto que hubo que descartar un gran número de piezas por problemas relacionados con grumos en el diámetro de la brida.
“Mi tarea consistió en conocer mejor los problemas del material y los obstáculos a los que nos enfrentábamos en la máquina.”
José “Pepe” Puchau
Antonio Díaz de Producción, Diego Rodríguez de Tecnología, Mariano Ramos de Control de Calidad, y Pepe Puchau de Tecnología, se encargaron de trabajar con los operarios de la máquina para resolver el problema. “Mi tarea consistió en conocer mejor los problemas del material y los obstáculos a los que nos enfrentábamos en la máquina. Profundizando y analizando la situación, el equipo encontró la solución”, señala Pepe Puchau.

El equipo interdepartamental de Museros que resolvió el problema
La solución fue reemplazar la placa de acero que se rompía tras cada 10.000 piezas. El equipo desarrolló una matriz de metal duro con el molde integrado de la placa. Dada la gran durabilidad de la placa, a Antonio se le ocurrió la idea de llamarla la “herramienta para siempre”. Ahora, con esta herramienta, el tiempo de ejecución de la máquina se ha multiplicado por quince y el equipo espera seguir aumentándolo.
Pepe Puchau: “Lo que más me ha impresionado del equipo es su motivación y sus ganas de hacer nuevas cosas y mejorar. Cuando las personas trabajan por conseguir un objetivo concreto, sacan lo mejor de sí mismos y ahí es cuando logramos grandes cosas. Involucrar a operarios y técnicos, aprender de ellos y hacer que a la gente le guste su trabajo: eso es algo que siempre me motiva”.
Homberg (Alemania)
Priorización automática del acero

El coordinador del equipo Andreas Fey priorizando el suministro del acero
Antes de prensar el acero en nuestras máquinas, normalmente debe ser sometido a dos procesos adicionales. En primer lugar, el alambrón debe ser tratado previamente en el sistema de tratamiento de materiales para garantizar que se eliminen todas las impurezas y sustancias no deseadas y, a continuación, debe aplicársele lubricante. Además, si el diámetro no fuera como debería ser, el siguiente paso consiste en trefilar el acero en una trefiladora para lograr el diámetro exacto requerido. Solo entonces, una vez hecho esto, puede pasarse al procesado de conformado en frío.
Hasta hace poco, el coordinador del equipo de la trefiladora de la planta de Homberg (Alemania) tenía que ir cada mañana al cockpit de SAP para ver qué alambrón se necesitaba (urgentemente) ese día para la prensadora y la trefiladora. Entonces, se priorizaba el alambrón de la lista de selección para garantizar que el sistema de tratamiento de materiales supiera qué material debía procesarse primero. Cada día había que dedicar aproximadamente tres horas al proceso de priorización del alambrón invirtiendo tiempo en planificar, realizar llamadas de teléfono y enviar correos electrónicos. Y, si algo se agotaba con poco tiempo de antelación, era difícil reemplazarlo por otro. Además, esta tarea afectaba a otras capacidades retrasando a su vez la ejecución de otras operaciones.
Junto con el equipo de nexineer, el equipo creó aquí un proceso en SAP que compara los datos del cockpit con los materiales disponibles y prioriza automáticamente las tareas necesarias. Gracias a ello, el software se encarga de realizar la parte más tediosa del trabajo y permite que el personal pueda dedicar ese tiempo a desempeñar sus funciones en sus respectivos departamentos.
Jintan (China)
Tutores entre plantas
La nueva planta de Jintan (China) se puso en marcha el tercer trimestre del año pasado, lo que fue motivo de alegría para los empleados de ambas plantas. En cuanto se empezó con la configuración general y la producción, el equipo se enfrentó a ciertos retos como a exigentes auditorías por parte de clientes y escasez de talento por la estructura industrial local. De hecho, este último se convirtió en el mayor reto para la nueva planta por la falta de operarios y técnicos cualificados, especialmente para los procesos de conformado en frío y roscado. Así pues, hubo que implementar un programa de tutorización entre las plantas. Este programa ha funcionado muy bien y se ha convertido en el primer paso caminado hacia el éxito.
La tutorización entre plantas implica ayudarse mutuamente entre las dos plantas. En esta etapa particular, esto se refiere principalmente a prestar apoyo en la fase de inicio de Jintan con especial atención a la formación cualificada de operarios de conformado en frío y roscado. Este programa de tutorización de dos meses comenzó en octubre. YANG Jinlong fue uno de los operarios recién contratados que se enviaron a Wujin. ZHANG Yi, con más de seis años de experiencia en conformado en frío en Wujin, fue designado como tutor de YANG. Aproximadamente un mes más tarde, llegó YU Xiaosuo, operario de roscado de Jintan que se convirtió en tutor de WANG Youwei de Wujin. Los tutores siguieron las instrucciones fijadas para las cuatro fases de la formación de los nuevos operarios:
- Yo hago y tú observas.
- Hazlo conmigo.
- Tú haces y yo observo.
- Seguimiento y rectificaciones.
El proceso y las máquinas de conformado en frío de KAMAX son un terreno completamente nuevo para estos empleados. La tutorización abarca todo el proceso desde la identificación de planos al control de calidad pasando por cambios de moldes o troqueles, ajustes de elementos de fijación, puesta a punto de la maquinaria y resolución de problemas. Debido a la alta demanda del cliente, en esta ocasión el tiempo de la formación junto a la máquina era limitado, por lo que cada minuto contaba. El esfuerzo conjunto de ambas plantas ha hecho posible mejorar la productividad en Jintan.
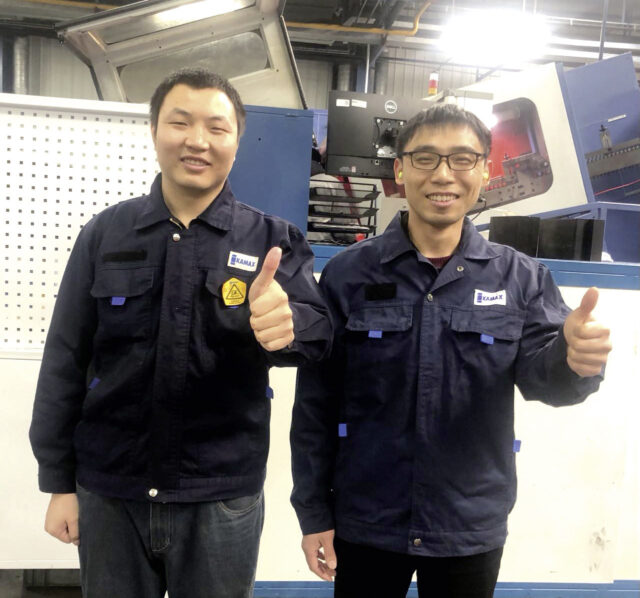
WANG Youwei y Zhang Yi, de diferentes plantas, ayudándose mutuamente
“Gracias al éxito de este programa de tutorización entre plantas, estamos pensando en convertirlo en un programa habitual cubriendo diferentes secciones entre dos plantas y aprovechar así las ventajas de diferentes equipos”.
YANG Liping (Laraine), director de Personal y Cultura Corporativa
Bardejov (Eslovaquia)
Bardejov apoya a Alemania
A finales del año pasado, se le pidió a nuestra planta de Bardejov (Eslovaquia) que ayudase a la planta de Osterade (Alemania) haciéndose cargo del conformado en frío y el proceso de temple de los pernos destinados a Scania y Daimler. El objetivo era liberar capacidad en las máquinas OP-OHA.
Dado que Bardejov tiene una configuración diferente, al equipo de diseño central se le ocurrió la idea de ensamblar el juego de herramientas del diseño telescópico modular de Bardejov y los diseños clásicos de Osterode. El objetivo era agilizar el proceso, reducir el tiempo de producción y evitar problemas con el diseño modular. Para ello, los compañeros del departamento de Diseño, tanto central como local, trabajaron con compañeros de TEC BAR y TEC OHA. Gracias a los resultados obtenidos, pudimos prensar los pernos para Daimler durante las vacaciones de Navidad y logramos enviar la cantidad requerida con la calidad requerida.
En la misma semana, intentamos prensar los pernos para Scania en un test de herramientas y lo logramos. Desafortunadamente, el juego de herramientas se dañó muy pronto por fallos de material. Como en el test se habían conseguido los parámetros necesarios pese a la rotura del juego de herramientas, optamos por pedir un repuesto para la pieza dañada. En la semana seis de este año, una vez recibido el repuesto, el equipo logró prensar con éxito más de 6.000 pernos en este ensamblaje. Y todo está preparado para seguir prensando. Anteriormente, no podían extraerse más de 3.000 pernos sin dañar el juego de herramientas previo.
Lapeer (Estados Unidos)
15 minutos al día
En Lapeer, algunos compañeros llevan ya casi dos semanas aprendiendo y practicando kata*.
“Es la parte más divertida del día”, destaca Chris Case, aprendiz del área de Producción. “Aún no sé cómo hacerlo, pero sé cómo conseguirlo”, sentencia Mike Freeman, entrenador experimentado de kata y aprendiz del área de Ingeniería.
Kata es una práctica diaria, un hábito, una rutina en la que un entrenador y un aprendiz realizan diariamente una sesión de entrenamiento de 15 minutos siguiendo un conjunto de cinco preguntas estándar para trabajar en la consecución de objetivos. La práctica de kata consiste en desarrollar una cultura de mentalidad científica escribiendo cada día el siguiente paso previsto que vamos a dar y qué esperamos de dar ese paso. Al día siguiente, se revisa lo que ocurrió durante ese paso y lo que hemos aprendido. No perdemos el tiempo intentando adivinar soluciones, sino que nos centramos en una metodología de “Mira y ve” que consiste en obtener primero una idea profunda de nuestra condición actual y, entonces, atravesar diariamente paso a paso por la incertidumbre para conseguir lo que necesitamos conseguir en el siguiente paso.
“Con respecto a la formación de entrenadores de kata, actualmente estamos implementando el programa de kata en otras sedes con la ayuda de Jon Sharp y OPEX. También estamos llevando a cabo el proceso de incorporación con nuestros compañeros de Europa y China, además de trabajar virtualmente desde Lapeer”, señala Ron Darling, ingeniero de producción de Lapeer.
* El término kata procede de las artes marciales japonesas y define con precisión secuencias de movimiento. Estas secuencias se internalizan y se convierten en rutina mediante la práctica y el uso de modo que acaban por realizarse reflexivamente sin tener que pensar en ellas.
Turnov (la República Checa)
Reciclar en vez de comprar
En los últimos años, la planta de Turnov (República Checa) ha sido la planta más rentable del grupo KAMAX. Si bien, aquí, igualmente no son siempre los proyectos y los hitos más grandes los que hacen el éxito de la sede, sino que a menudo es la unión de los efectos de todas las optimizaciones y mejoras pequeñas. El procesamiento de herramientas usadas es un buen ejemplo de ello.
En vez de reemplazar las herramientas usadas por otras nuevas, Václav Šantin y su equipo de Turnov analizaron todas las herramientas que habían estado usando en las máquinas para ver cuáles podrían ser reparadas y reutilizadas. El equipo comparó las herramientas menos dañadas del descarte con la lista de pedidos de nuevas herramientas cotejando planos y documentación de las herramientas. De este modo, si una herramienta se consideraba apta, se reparaba, se adaptaba, se sometía a una inspección y se etiquetaba con la denominación “RETRABAJADA”.
Así, en vez de pedir nuevas herramientas, esas herramientas “RETRABAJADA” se volvían a utilizar para trabajar en las máquinas. Solo cuando la utilidad de las herramientas reparadas bajaba de un umbral específico, se retiraban del proceso. Durante el año pasado, el equipo de Václav consiguió ahorrar más de 50.000 € (incluido el coste de las reparaciones) gracias a este proceso de reciclado de piezas descartadas.
Evidentemente, estos seis proyectos no son más que una pequeña muestra del mundo KAMAX, pero dejan patente algo muy claro: los pequeños éxitos se traducen en algo más grande. Y solo si seguimos teniendo realmente ganas, seguimos eliminando los errores de nuestro trabajo diario, continuamos aspirando a cambiar los procesos de forma que faciliten nuestro trabajo y nos ayudamos mutuamente con nuestro conocimiento y experiencia, seguiremos siendo una compañía de éxito.
KXpress