Malé úspechy sa premietajú do väčších
Pravidelne oslavujeme veľké aj malé úspechy, ktoré majú vplyv na naše závody, či už ide o zlepšenia alebo nové projekty. Preto sa toto číslo zameriava na ľudí, ktorí zabezpečujú hladký priebeh našej každodennej výroby a na to, aby sme čoraz menej času trávili „hasením požiarov“.
Či už je to v Španielsku, Nemecku, Číne, Mexiku, Českej republike, USA alebo na Slovensku, nespočetné množstvo našich kolegov pracuje deň čo deň na optimalizácii a zjednodušení našich procesov. Ich úspechy sú neuveriteľne rôznorodé: minimalizácia opotrebovania nástrojov, podpora tímov z iných závodov, zvýšenie produktivity lisu, vytvorenie nových komunikačných kanálov medzi oddeleniami alebo jednoducho dobrá a čistá práca.
Nebyť úsilia týchto ľudí, spoločnosť KAMAX ako celok by nikdy nemala taký úspech a naša spoločnosť by zanikla bez stopy už pred desiatkami rokov. Vo firme s takmer 4 000 zamestnancami by bolo prakticky nemožné predstaviť každý z týchto projektov a ľudí. Napriek tomu sme sa snažili zahrnúť reprezentatívny výber úspešných príbehov z rôznych miest. Niektoré z nich sú väčšie ako iné, ale všetky majú jedno spoločné: vďaka nim sa spoločnosť KAMAX posunula vpred.

Jeden malý krok z mnohých na svete: repasovanie nástrojov v Turnove (Česká republika)
Museros (Španielsko)
Večný nástroj
Porucha stroja je jedným z najviac nepríjemných problémov vo výrobe; môže rýchlo spôsobiť ďalšie komplikácie a musí sa bezodkladne vyriešiť. Príkladom toho bol pred niekoľkými mesiacmi Museros (Španielsko). Problém s poruchami spôsobil zastavenie výroby modelu NEDSCHROEF NB515-1 po množstve 10 000 vyrobených dielov. Bolo potrebné nájsť riešenie z hľadiska kvality, keďže sa pre problémy s hrudkami materiálu v priemere príruby vyraďoval vysoký počet dielov.
„Mojou úlohou bolo zistiť viac o problémoch s materiálom a o prekážkach, ktorým sme pri stroji čelili.“
José „Pepe“ Puchau
Na spoluprácu s operátormi strojov pri riešení problému boli priradení Antonio Díaz z výroby, Diego Rodriguez a José Puchau z technologického oddelenia, Marino Ramos z riadenia kvality. „Mojou úlohou bolo zistiť viac o problémoch s materiálom a o prekážkach, ktorým sme pri stroji čelili. Vďaka hlbšiemu pohľadu a analýze situácie našiel tím správne riešenie,“ povedal José „Pepe“ Puchau.

Úspešne vyriešil problém: medzirezortný tím spoločnosti v Muserose
Riešením bola výmena oceľového plechu, ktorý sa lámal po každých 10 000 dieloch. Tím vyvinul tvrdú kovovú matricu s integrovaným tvarom dosky. Vzhľadom na vysokú odolnosť dosky prišiel Antonio s nápadom nazvať ju „večný nástroj“. Čas prevádzky stroja sa vďaka tomuto nástroju zvýšil 35-krát a dúfajú, že sa ešte zvýši.
Jose „Pepe“ Puchau: „Najviac na mňa zapôsobila motivácia a túžba robiť nové veci a zlepšovať sa. Keď ľudia pracujú na dosiahnutí správneho cieľa, vydávajú zo seba to najlepšie, a vtedy sa nám daria úžasné veci. Zapájať operátorov a technikov, učiť sa od nich a pomáhať ľuďom, aby mali radi svoju prácu, to je to, čo ma vždy motivuje.“
Homberg (Nemecko)
Automatické určenie priority drôtov

Hovorca tímu Andreas Fey má dodávky drôtov ako prioritu.
Pred lisovaním drôtu na našich strojoch musí drôt zvyčajne prejsť ďalšími dvoma procesnými krokmi. Drôt sa musí vopred upraviť v systéme na úpravu materiálu, aby sa zabezpečilo odstránenie všetkých nečistôt a nežiaducich látok, a potom sa musí naniesť mazivo. V prípade, že priemer stále nie je úplne taký, aký by mal byť, je ďalším krokom pretiahnutie ocele, aby sa dosiahol presný požadovaný priemer. Až potom, po týchto úkonoch, je čas na proces tvarovania za studena.
Donedávna musel zástupca tímu z ťahárne v závode Homberg (Nemecko) každé ráno chodiť do „pracovnej kabíny“ v systéme SAP, aby zistil, ktorý drôt v ten deň (naliehavo) potrebujú v lisovni a ťahárni. Potom určili priority drôtu v „zozname na výber“, aby sa zabezpečilo, že systém spracovania materiálu na vyššej úrovni bude vedieť, ktorý materiál sa má spracovať ako prvý. Každý deň bolo potrebné venovať približne tri hodiny procesu určovania priorít, išlo o čas strávený plánovaním, telefonovaním a posielaním e-mailov. Vždy, keď niečo zrazu vypadlo, bolo ťažké to nahradiť. Okrem toho táto úloha viazala kapacity na iných miestach, čo následne zdržiavalo vykonávanie iných operácií.
Spolu s tímom Nexineer tu vytvorili proces v rámci SAP, ktorý porovnáva údaje z „pracovnej kabíny“ s materiálom na sklade a automaticky určuje priority potrebných úloh. Softvér tak dokáže prevziať nudnú časť práce, vďaka čomu majú ľudia viac času na svoje hlavné povinnosti v príslušných oddeleniach.
Jintan (Čína)
Systém medzizávodných kamarátov
Nový závod v Jintane (Čína) je v prevádzke od tretieho štvrťroka minulého roka, čo všetci zamestnanci oboch závodov prijali s veľkým nadšením. Keď tím začal s celkovým nastavením a výrobou, narazil na problémy, ako napríklad náročné zákaznícke audity a obmedzené zdroje talentov v dôsledku štruktúry miestneho priemyslu. Z toho vyplynula najväčšia výzva pre nový závod – nedostatok kvalifikovaných operátorov a technikov, najmä na lisovanie a na valcovanie závitov. Preto sa zaviedol systém „kamarátov“ medzi jednotlivými závodmi. Ten sa osvedčil a je to prvý krok k úspechu.
Systém kamarátov medzi závodmi znamená vzájomnú podporu medzi našimi dvoma závodmi. V tejto konkrétnej fáze sa to týka najmä podpory nábehu v Jintane zameranej na odbornú prípravu operátorov na tvarovanie za studena a na valcovanie závitov. Dvojmesačný mentorský projekt sa začal v októbri. YANG Jinlong bol jedným z novoprijatých operátorov vyslaných do Wujinu. ZHANG Yi, ktorý má viac ako šesť rokov skúseností s tvarovaním za studena vo Wujine, vymenovaný za Yangovho tútora. Približne po mesiaci prišiel druhý pár kamarátov: YU Xiaosuo, operátor TR z Jintanu, a tútor WANG Youwei z Wujinu tiež začali svoju novú cestu. Tútori postupovali podľa pokynov pre štvorstupňové školenie nových operátorov:
- Ja robím, ty sa pozeraj.
- Rob to spolu so mnou.
- Ty rob, ja sa pozerám.
- Sledovanie a náprava.
Proces tvarovania za studena a stroje spoločnosti KAMAX sú pre týchto zamestnancov úplne novou činnosťou. Učebné materiály sa týkali všetkého od rozpoznávania výkresov až po meranie kvality, výmeny výliskov a dierovačov, nastavenia prípravkov, bežného dolaďovania stroja a odstraňovania problémov. Pre veľký dopyt zákazníkov bol čas na zaškolenie na stroji obmedzený, preto bola každá minúta dôležitá. Spoločné úsilie oboch závodov umožnilo zvýšiť produktivitu v Jintane.
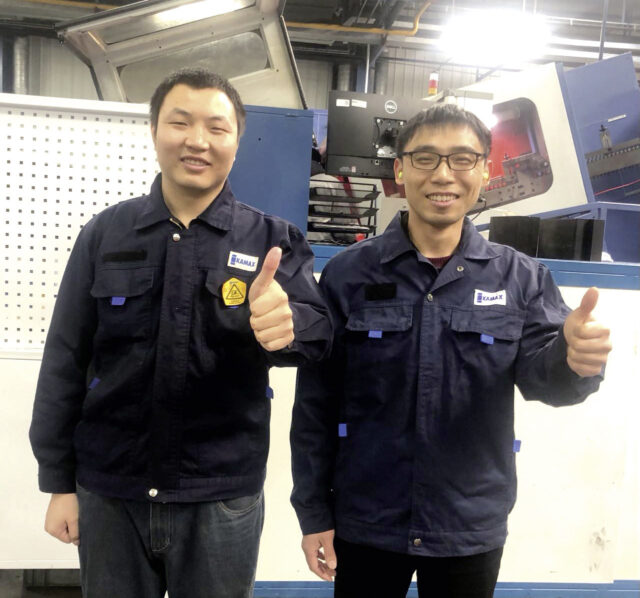
Kamaráti z rôznych závodov WANG Youwei a Zhang Yi
„Vďaka úspechu tohto systému medzizávodných kamarátov plánujeme z neho urobiť rutinný program, ktorý bude pokrývať rôzne úseky medzi dvoma závodmi, aby sa maximalizovali výhody rôznych tímov.“
Yang Liping (Laraine), manažérka pre ľudí a kultúru
Bardejov (Slovensko)
Bardejov podporuje Nemecko
Koncom minulého roka bol náš závod v Bardejove (Slovensko) požiadaný, aby podporil výrobu v Osterode (Nemecko) tým, že prevezme tvarovanie za studena a tepelné spracovanie spojovacích prvkov pre spoločnosti Scania a Daimler. Cieľom bolo uvoľniť kapacitu na strojoch OP-OHA.
Vzhľadom na odlišné nastavenie v Bardejove prišiel centrálny konštrukčný tím s nápadom zostaviť súpravu nástrojov modulárnej „teleskopickej“ konštrukcie v Bardejove a klasických konštrukcií z Osterode. Cieľom bolo urýchliť proces, skrátiť čas výroby a vyhnúť sa nevyriešeným problémom s modulárnou konštrukciou. Kolegovia z konštrukčného oddelenia, centrálneho aj miestneho, spolupracovali s kolegami z TEC BAR a TEC OHA. Vďaka tomu sme počas vianočných sviatkov úspešne lisovali spojovacie prvky pre spoločnosť Daimler. Dodali sme požadované množstvo v náležitej kvalite.
V tom istom týždni sme vyskúšali lisovanie spojovacích prvkov pre spoločnosť Scania ako skúšku nástroja, ktorá bola úspešná. Bohužiaľ, súprava nástrojov sa veľmi skoro rozbila, pretože bol chybný materiál. Keďže test úspešne dosiahol požadované parametre aj napriek praskline v súprave nástrojov, začali sme objednávať náhradný diel za ten poškodený. V šiestom týždni tohto roka, po dodaní náhradného dielu, tím na tejto zostave úspešne nalisoval viac ako 6 000 dielov. Stroj je pripravený na ďalšie lisovanie. V histórii tohto konkrétneho dielu nebolo možné vyrobiť viac ako 3 000 skrutiek bez poškodenia predchádzajúcej nástrojovej zostavy.
Lapeer (USA)
15 minút denne
V Lapeeri sa niektorí kolegovia učia cvičenia Kata* a krok za krokom experimentujú už takmer dva roky. A to s veľkým úspechom.
„Je to najzábavnejšia časť môjho dňa,“ povedal Chris Case, skúsený žiak a zlepšovateľ vo výrobe. „Momentálne neviem, ako to dosiahnuť, ale viem, ako sa k tomu dostať,“ povedal Mike Freeman, skúsený tréner Kata a študent inžinierstva.
Kata je každodenná prax, zvyk, rutina, pri ktorej sa kouč a žiak každý deň 15 minút venujú dennému cyklu koučovania podľa štandardného súboru piatich otázok, pomocou ktorých sa chcú dopracovať k úspechu. V praxi ide o rozvoj kultúry vedeckého myslenia tým, že si každý deň zámerne napíšeme ďalší krok a to, čo od neho očakávame, a potom nasledujúci deň prehodnotíme, čo sa počas tohto kroku stalo a čo sme sa naučili. Netrávime čas hádaním riešení, ale sa skôr zameriavame na metodiku „choď a uvidíš“, pri ktorej najprv do hĺbky pochopíme náš súčasný stav a potom sa každý deň krok za krokom pohybujeme v neistote, aby sme dosiahli to, čo potrebujeme dosiahnuť ďalej.
„Pokiaľ ide o školenie koučov Kata, v súčasnosti s pomocou Jona Sharpa a OPEX zavádzame program Kata v ďalších lokalitách. Zapájame aj našich kolegov v Európe a Číne a virtuálne pôsobíme z Lapeeru,“ povedal Ron Darling, výrobný inžinier v Lapeeri.
* Pojem Kata pochádza z japonských bojových umení a označuje podrobnú definíciu sekvencie pohybov. Cvičením a aplikáciou sa stávajú takými rutinnými a zvnútornenými, že ich vykonávame takmer reflexívne bez premýšľania.
Turnov (Česká republika)
Recyklácia namiesto nákupu
Turnov (Česká republika) je v posledných rokoch najziskovejším závodom skupiny KAMAX. Aj tu však platí, že nie vždy sú to veľké projekty a medzníky, ktoré robia lokalitu úspešnou. Namiesto toho ide často o kombinovaný účinok všetkých malých zlepšení a optimalizácií. Dobrým príkladom je proces pre použité nástroje.
Namiesto výmeny použitých nástrojov za nové Václav Šantin a jeho tím v Turnove najprv zhodnotia všetky nástroje, ktoré sa už v strojoch použili, aby získali prehľad o tom, ktoré z nich by mohli byť skutočne vhodné na opravu a opätovné použitie. Tím potom porovnáva menej poškodené diely zo „šrotu“ na základe výkresov a dokumentácie so zoznamom objednávok nových nástrojov. Ak je použitý nástroj vhodný, opraví sa, upraví a po následnej kontrole sa označí ako „REPAS“.
Namiesto objednávania nových nástrojov sa tieto nástroje s označením „REPAS“ opäť nasadia do strojov. Až keď užitočnosť opravených nástrojov klesne pod určitú hranicu, vyradia sa z procesu. Za posledný rok sa Václavovmu tímu podarilo recykláciou „šrotu“ ušetriť viac ako 50 000 EUR, a to aj po úhrade nákladov na opravy.
Týchto šesť projektov je zjavne len malou vzorkou zo sveta spoločnosti KAMAX, ale veľmi jasne ukazujú jednu vec: malé úspechy sa premietajú do niečoho väčšieho. A len ak budeme javiť záujem a budeme pracovať na odstraňovaní drobných chýb v našej každodennej práci, budeme sa naďalej snažiť meniť procesy tak, aby sme si uľahčili prácu a budeme si navzájom pomáhať svojimi vedomosťami a skúsenosťami, zostaneme úspešnou spoločnosťou.
KXpress