Immer eine
Entwicklung
voraus
Damit unsere Schrauben und Formteile ihre Aufgabe erfüllen können, kommt es sowohl auf den Stahl als auch auf seine Beschichtung an. Wir zeigen, welche Entwicklungsarbeit dahintersteckt, alle Kundenwünsche zu erfüllen und der Konkurrenz voraus zu sein.
Wenn wir KAMAX mit Wettbewerbern vergleichen, dann stechen wir vor allem durch unsere Application Engineering-Expertise und unsere Forschungs- & Entwicklungsarbeit hervor. Genauer gesagt: ein Produkt für unseren Kunden zu erschaffen, das exakt auf seine Bedürfnisse zugeschnitten ist und sehr ausgiebig getestet wurde. Um neue Ideen umzusetzen und zu prüfen, sind unsere Labore bestens ausgestattet: mit einer Versuchspresse, Korrosionskammern, Metallographie und diversen Prüfeinrichtungen zur Ermittlung von Materialeigenschaften, Reibungskoeffizienten sowie vielem mehr.
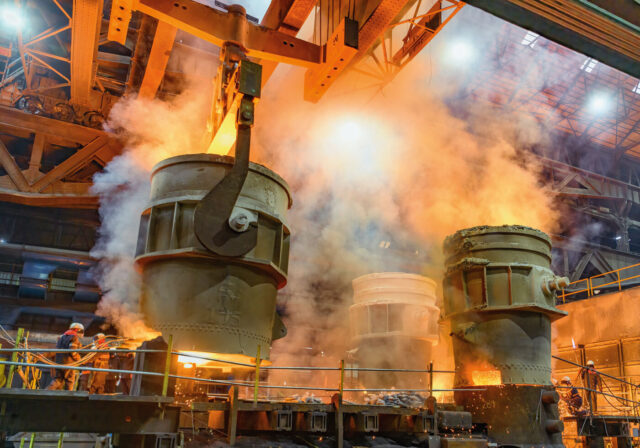
Wir arbeiten eng mit den Stahlherstellern zusammen, um unser Rohmaterial weiterzuentwickeln.
Schrauben ohne Wärmebehandlung
Ein Entwicklungsprojekt, für das diese Laborausstattung zum Einsatz kommt, ist KXGreen. Das Pariser Klimaabkommen fordert uns und unsere Zulieferer und Kunden: Nachhaltige Produkte, weniger Energieverbrauch und „grüner“ Stahl sind gefragt. Das Projekt zielt darauf ab, Schrauben ohne vergütende Wärmebehandlung herstellen zu können. Der aktuelle Stand? „Die Anforderungen, die heute an konventionell erzeugte Schrauben gestellt werden, erfüllen wir noch nicht alle zu 100 %. Die Abweichungen sind aber nur gering“, sagt Dr. Christian Schnatterer, Entwicklungsingenieur für Stahl bei Business Product and Process Development (BPD). Gleichzeitig ist das Potenzial riesig, denn die Wärmebehandlung ist sehr energieintensiv und verursacht durch das Verbrennen von Gas viele CO₂-Emissionen. „Am Ende wollen wir unsere Kunden überzeugen. Das kann funktionieren, indem wir das Produkt immer weiter verbessern und die Kundenseite sich öffnet für neue Technologien“.
Derzeit entwickeln die Kolleginnen und Kollegen außerdem einen Prüfstand, der Verbindungselemente hinsichtlich Wasserstoffversprödung noch detaillierter als bisher unter die Lupe nimmt. Gerade bei ultrahochfesten Schrauben, die aufgrund ihres geringeren Gewichts und der besseren CO₂-Bilanz immer beliebter werden, ist das eine Gefahr. Wasserstoffversprödung kann zu einem schlagartigen Bauteilversagen führen, falls beispielsweise infolge einer Korrosionsreaktion Wasserstoff in die Schraube eindringt. Es braucht also einen besonderen Stahl, und der ist teuer. Deshalb forscht KAMAX gemeinsam mit einem Stahlhersteller nach einer kostengünstigeren Alternative. Christian Schnatterer: „Es ist faszinierend, dass wir als KAMAX auf Augenhöhe mit technologisch führenden Stahlherstellern Werkstoffe entwickeln. Gemeinsam mit unseren Stahllieferanten passen wir unsere Werkstoffe immer wieder an, bis sie unseren Anforderungen entsprechen.“
Dass es sich lohnt, zeigt die Erfolgsgeschichte von thermomechanisch gewalztem Draht. Bei diesem Verfahren wird die gute Umformbarkeit des Drahtes durch eine spezielle Prozessführung beim Walzen erreicht. Das übliche nachgelagerte Glühen entfällt, was den Prozess deutlich energieeffizienter macht. Bis der Prozess wie gewünscht funktionierte, dauerte es mehrere Jahre, heute ist er bei uns Standard.
Christian Schnatterer und Holger Lamm
Ein Mix aus bis zu 50 Stoffen
Ist der Stahl erstmal zum Verbindungselement geformt, geht es darum, die ideale Beschichtung für die Verschraubung beim Kunden zu finden. Eine Aufgabe, die nur Chemiker*innen meistern können, denn eine Beschichtung ist eine Mixtur aus bis zu 50 Reinstoffen. Diese beeinflussen sich gegenseitig und machen es komplex, das richtige Verhältnis für die gewünschten Eigenschaften zu schaffen. „Das ist wie bei einem Curry“, verdeutlicht Holger Lamm, der als Beschichtungsexperte bei BPD die Entwicklung neuer Oberflächen vorantreibt. „Nehme ich mehr Koriander dazu, verändert sich das gesamte Mischverhältnis und ich muss aufpassen, dass das Curry nicht zu einseitig schmeckt.“
Neue Mischungen müssen gerade jetzt entwickelt werden, da die Europäische Union weitreichende Beschränkungen von sogenannten PFAS plant. PFAS sind per- und polyfluorierte Alkylverbindungen. Diese besonders langlebigen chemischen Stoffe kommen bei etwa 70 % der KAMAX-Produkte in Beschichtungen zum Einsatz. Auch wenn noch offen ist, wie die Gesetzeslage am Ende aussieht, gilt es, auf alle Eventualitäten vorbereitet zu sein. Hier kommt es auf die Zusammenarbeit mit den Lieferanten an. „Vielleicht gibt es schon Alternativen, wenn ja, testen wir diese, stellen sie Kunden vor und zertifizieren“, erklärt Holger Lamm. Gibt es keinen Ersatz und auch keinen anderen Hersteller, müssen die Kollegen selbst ran. „Das chemische Know-how dafür haben wir!“
Im Zentrum steht bei der Entwicklung neuer Beschichtungen auch immer der Kunde: die Oberfläche verändert den Reibwert und die Wahrscheinlichkeit einer Korrosion der Schraube. Ebenfalls gefordert sind immer mehr nachhaltige Stoffe. „Als ich vor fast 40 Jahren angefangen habe, ging es in erster Linie darum, das technische Ziel zu erreichen. Heute ist mindestens ebenso wichtig, wie umweltverträglich eine Beschichtung ist und wie energieeffizient ich sie aufbringen kann.“

Overview of different coatings
Pulverbeschichtung & biobasierte Rohstoffe
Vielversprechend ist zum Beispiel der Einsatz von Pulverbeschichtungen, da diese eine hohe Recyclingquote aufweisen. Immer häufiger kommen auch biobasierte Rohstoffe zum Einsatz. Wasserstoff als Energiequelle oder neue Einsatzgebiete der KAMAX’schen Verbindungselemente außerhalb der Automobilindustrie stellen ebenfalls neue Anforderungen. Das alles sind Themen, welche die Ingenieur*innen und Chemiker*innen bei ihrer Entwicklungsarbeit auch in den nächsten Jahren noch auf Trab halten werden. Die neusten Entwicklungen bleiben dabei noch unter Verschluss, da die Projekte noch nicht abgeschlossen sind.
Um überhaupt dahin zu kommen, braucht es Durchhaltevermögen und Veränderungswillen. Die Entwicklung einer neuen Beschichtung dauert schnell mal zwei Jahre, eine neue Stahlsorte zu entwickeln, die ein spezielles Eigenschaftsprofil aufweist, noch deutlich länger. Daher benötigt es die Bereitschaft, nach einem Misserfolg weiterzumachen. „Klar kann es auch mal frustrierend sein, wenn im Labor nicht das gewünschte Ergebnis herauskommt. Aber auch daraus lernen wir“, sagt Christian Schnatterer. Und das seit über 85 Jahren: Denn KAMAX Gründer Rudolf
Kellermann war selbst Pionier und wandte bereits von Beginn an Prüf- und Labortechniken an. Er setzte früher als andere auf die wissenschafts-orientierte Entwicklung der Schraube und des Werkstoffs.
nach 720 Stunden

Um eine neu entwickelte Beschichtung zu testen, wenden wir verschiedene Verfahren an. Die gezeigten Teile waren im beschleunigten Korrosionstest (gemäß Volvo STD 423-0014). Dabei kommt es zu einem Wechselspiel zwischen Temperatur (von 35°C bis 45°C) und Feuchtigkeit (von 50 % bis 95 %). Außerdem findet zweimal wöchentlich eine Sprühphase statt, die 45 Minuten dauert. Zu diesem Zweck wird eine Flüssigkeit (Gemisch aus entionisiertem Wasser, Salz und Schwefelsäure) durch drei Düsen im System geleitet und versprüht. Insgesamt wurden sie dem Test 4 Wochen lang ausgesetzt.
KXpress