Always
one step
ahead
When it comes to ensuring that our bolts and form parts can do their job, both the steel and the coating are important. We will show you the development work that is required for us to satisfy all our customers’ needs – and stay one step ahead of the competition.
When we compare KAMAX with its competitors, it is especially notable for the way in which we apply our engineering expertise and for our research and development work. To be more precise: KAMAX stands out for its ability to create products that are tailored to our customers’ needs and requirements – products that have also been extensively tested. Our laboratories are perfectly equipped to implement and evaluate new ideas, with a test press, corrosion chambers, metallography, and various testing equipment and facilities available for determining material properties, friction coefficients, and many other characteristics.
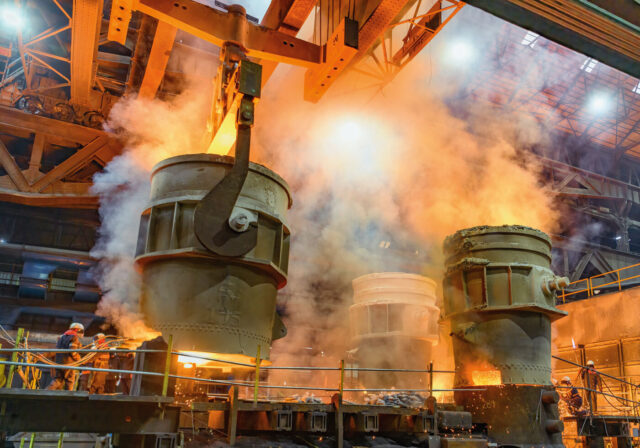
We work closely with the steel manufacturers in order to continuously develop our raw material
Bolts without heat treatment
One innovative project for which this laboratory equipment is used is KXGreen. The Paris Climate Agreement demands a great deal of KAMAX and its suppliers and customers: sustainable products, reduced energy consumption, and “green” steel. The goal of this project is to produce bolts without any need for heat treatment to temper them. Its current status? “We are not yet able to fully satisfy all of the requirements for conventionally produced bolts. The remaining deficiencies, however, are minor,” says Dr. Christian Schnatterer, Development Engineer for Steel in Business Product and Process Development (BPD). At the same time, there is tremendous potential here because heat treatment is very energy-intensive and causes a high level of CO₂ emissions due to the gas that must be consumed. “We aim to combine further technical improvements with the necessary openness to technologies in the marketplace to demonstrate the benefits of our technology for our customers.”
Our colleagues are also in the process of developing a test bench that is capable of even more detailed examinations of fasteners regarding hydrogen embrittlement than in the past. This is a particular danger for ultra-high-strength bolts – thanks to their lower weights and smaller CO₂ footprints, these bolts are increasingly popular. Hydrogen embrittlement can lead to the sudden failure of components, for example, if corrosion allows hydrogen to enter the bolt. This means special steel is required, and this is expensive. That is why KAMAX is working with a steel producer to find a cost-effective alternative. Christian Schnatterer: “I find it fascinating that we are able to develop materials here at KAMAX that are every bit as good as those produced by the technologically leading steel producers. We work continuously with our steel suppliers to adapt our materials until they can satisfy our requirements.”
The success of thermomechanically rolled wire shows that this is all worthwhile. In this process, the wire’s good formability is achieved by specially configuring the rolling process. The conventional downstream annealing is eliminated, making the process significantly more efficient. It took years before the process worked as intended, but today, it is standard practice at KAMAX.
Christian Schnatterer and Holger Lamm
A mix of as many as 50 materials
Once the steel has been formed into a fastener, the goal is to determine the ideal coating for the fastening at the customer. This task can only be done properly by chemists because a coating is a mixture of as many as 50 pure substances. These influence one another, so it is a complex process to determine the correct ratio of each ingredient to achieve the desired properties. Holger Lamm, a coating expert at BPD who is driving the development of new surfaces, stresses this point: “It’s a bit like a curry. If I add more cilantro, this changes the entire mixture, and I have to be careful that the curry is not dominated by one particular flavor.”
New mixtures must be developed now because the European Union is planning far-reaching restrictions on what are known as PFAS, or perfluoroalkyl and poly-fluoroalkyl substances. These chemical substances are particularly long-lasting and are utilized in coatings in approximately 70 percent of KAMAX products. Although it is not yet clear what form the final legislation will take, the company must be prepared for any eventuality. This is an area where cooperation with suppliers is essential. As Holger Lamm explains: “Perhaps there are already alternatives – if so, we test these, present them to the customer, and certify them.” If there are no replacements or other manufacturers, our colleagues must take care of it themselves: “We have the necessary chemical expertise!”
When developing new coatings, the focus is always on the customer: the surface changes the friction coefficient and, therefore, the probability of the bolt corroding. There is also a growing need for more sustainable materials. “When I started nearly 40 years ago, the primary concern was always to achieve the desired technical specifications. Today, at least equal weight is given to just how environmentally friendly a coating is and how energy-efficient the application is.”

Overview of different coatings
Powder coating & biobased materials
One promising approach involves the use of powder coatings, because these have a high recycling rate. Also, biobased materials are being used more frequently. Other new challenges include hydrogen as a source of energy and new areas of application for KAMAX fasteners outside of the automotive industry. These are issues that will continue to occupy engineers‘ and chemists’ development work for years to come.
Staying power and a willingness to change are essential if we are going to reach our goals. Developing a new coating can easily take two years while creating a new type of steel with a particular set of properties requires considerably longer. That is why it is essential that people are ready to keep moving forward even after an attempt has failed. “It goes without saying that it can be frustrating when you don’t get the results you’re looking for in the lab, but we can also learn from these experiences,” says Christian Schnatterer. We’ve been doing this for more than 85 years – that is because KAMAX’s founder Rudolf Kellermann was himself a pioneer, and he employed testing and laboratory methods right from the start. He was ahead of the pack in utilizing scientific methods to develop fasteners and materials.
after 720 hours

To test a newly developed coating we use various procedures. The parts shown were in the Accelerated Corrosion Test (according to Volvo STD 423-0014). This involves an interplay between temperature (from 35°C to 45°C) and humidity (from 50% to 95%). Furthermore, a spraying phase takes place twice a week, which lasts 45 minutes. For this purpose, a liquid (mixture of deionized water, salt and sulphuric acid) is passed through three nozzles in the system and sprayed. In total, they were exposed to the test for 4 weeks.
KXpress