Siempre
un paso
adelante
Cuando se trata de asegurar que nuestros tornillos y piezas de conformado cumplen su función, tanto el acero como el revestimiento son importantes. Os mostraremos el trabajo de desarrollo que necesitamos poner en práctica para satisfacer todas las necesidades de nuestros clientes y mantenernos por delante de la competencia.
Cuando comparamos KAMAX con sus competidores, se destaca especialmente la forma en que aplicamos nuestros conocimientos de ingeniería y por nuestra labor de investigación y desarrollo. Para ser más precisos: KAMAX se diferencia de los demás por su habilidad para crear productos que están adaptados a las necesidades y requisitos de nuestros clientes, productos que también se han sometido a pruebas exhaustivas. Nuestros laboratorios están perfectamente equipados para implementar y evaluar nuevas ideas. Con una prensa de ensayos, cámaras de corrosión, metalografía y diversos equipos e instalaciones de ensayo disponibles, podemos determinar las propiedades de los materiales, los coeficientes de fricción y muchas otras características.
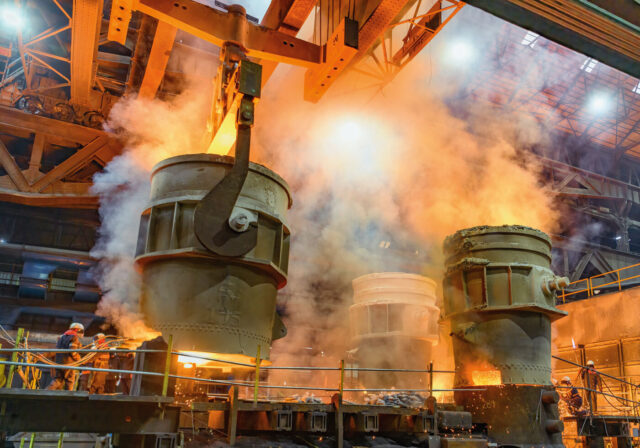
Colaboramos estrechamente con los fabricantes de acero para desarrollar nuestra materia prima de manera continua y estar un paso por delante de la competencia.
Tornillos sin tratamiento térmico
Un proyecto innovador para el que se usa este equipo de laboratorio es KXGreen. El Acuerdo de París sobre el cambio climático impone exigencias a KAMAX y a sus proveedores y clientes: productos sostenibles, reducción del consumo energético y acero “verde”. El objetivo de este proyecto es producir tornillos sin la necesidad del tratamiento térmico para templarlos. ¿Cuál es el estado actual? “Aún no podemos cumplir con todos los requisitos impuestos para los tornillos que se producen de manera convencional. Sin embargo, las deficiencias restantes son mínimas”, indica el Dr. Christian Schnatterer, Ingeniero del acero para el desarrollo de productos y procesos comerciales (BPD). Al mismo tiempo, existe un gran potencial, dado que el tratamiento térmico requiere mucha energía y emite grandes niveles de CO₂ a causa del gas que se debe consumir. “Nuestro objetivo es combinar nuevas mejoras técnicas con la apertura necesaria a las técnicas del mercado para demostrar los beneficios de nuestra tecnología a nuestros clientes”.
Nuestros compañeros también están desarrollando un banco de pruebas capaz de realizar exámenes aún más detallados de los elementos de fijación en relación con la fragilización por hidrógeno que en el pasado. Esto supone un peligro especial para los tornillos ultrarresistentes, cada vez más populares gracias a su menor peso y a su menor huella de CO₂. La fragilización por hidrógeno puede provocar el fallo repentino de componentes, por ejemplo, si la corrosión permite la entrada de hidrógeno en el tornillo. Esto significa que se requiere un acero especial, y es caro. Por este motivo, KAMAX está trabajando con un productor de acero para encontrar una alternativa rentable. Christian Schnatterer: “Me parece fascinante que podamos desarrollar materiales aquí en KAMAX que son tan buenos como los de productores de acero líderes desde el punto de vista tecnológico. Trabajamos continuamente con nuestros proveedores de acero para adaptar nuestros materiales hasta que puedan satisfacer nuestros requerimientos”.
El éxito del alambre laminado termomecánicamente demuestra que todo esto merece la pena. En este proceso, la buena conformabilidad del alambre se consigue configurando especialmente el proceso de laminado. Se elimina el recocido posterior convencional, lo que hace que el proceso sea mucho más eficaz. Llevó años para que el proceso funcionara como estaba previsto, pero hoy, es una práctica estándar en KAMAX.
Christian Schnatterer y Holger Lamm
Una mezcla de hasta 50 materiales
Una vez que el acero se ha conformado en un elemento de fijación, el objetivo es determinar el revestimiento ideal para el elemento de fijación en el cliente. Sólo los químicos pueden llevar a cabo esta tarea de forma adecuada, ya que un revestimiento es una mezcla de unas 50 sustancias puras. Estas sustancias dependen una de la otra, lo que por lo que determinar la proporción correcta de cada ingrediente para conseguir las propiedades deseadas es un proceso complejo. Holger Lamm, un experto en revestimiento en BPD que está impulsando el desarrollo de nuevas superficies, hace hincapié en este punto: “Es un poco como el curry. Si añado más cilantro, cambia toda la mezcla, y tengo que tener cuidado de que el curry no tenga un solo sabor dominante”.
Se deben desarrollar nuevas mezclas porque la Unión Europea planea restricciones de gran alcance sobre las llamadas PFAS, o sustancias perfluoroalquiladas y polifluoroalquiladas. Estas sustancias químicas son particularmente duraderas y se utilizan en los revestimientos de aproximadamente el 70 % de los productos de KAMAX. Si bien no está del todo claro cómo será la legislación final, la empresa debe estar preparada para cualquier eventualidad. Esta es un área en la que la cooperación con los proveedores es fundamental. Como explica Holger Lamm: “Quizás ya hay alternativas. De ser así, las analizamos, se las presentamos al cliente y las certificamos”. Si no existen reemplazos u otros fabricantes, nuestros compañeros deben ocuparse: “¡Tenemos la experiencia química necesaria!”.
Al desarrollar nuevos revestimientos, el enfoque está puesto siempre en el cliente: la superficie cambia el coeficiente de fricción y, por lo tanto, la probabilidad de que el tornillo se corroa. También existe una necesidad en aumento de más materiales sostenibles. “Cuando comencé hace casi 40 años, la preocupación principal era siempre alcanzar las especificaciones técnicas deseadas. Hoy en día, se le da al menos la misma importancia a qué tan respetuoso con el medioambiente es el revestimiento y qué tan eficiente energéticamente es la aplicación”.

Resumen de los distintos revestimientos.
Revestimiento en polvo y materiales de base biológica
Un enfoque prometedor es el uso de revestimientos en polvo, que tienen un alto índice de reciclado. También se están utilizando con más frecuencia los materiales de base biológica. Otros nuevos desafíos incluyen el hidrógeno como fuente de energía y nuevas áreas de aplicación de los elementos de fijación de KAMAX fuera de la industria automovilística. En los próximos años, el trabajo de desarrollo de los ingenieros y los químicos se seguirá centrando en estas cuestiones.
La fuerza de voluntad y la disposición al cambio son esenciales para alcanzar nuestros objetivos. Desarrollar un nuevo revestimiento puede llevar fácilmente dos años, mientras que crear un nuevo tipo de acero con un conjunto particular de propiedades puede llevar muchísimo más tiempo.Por eso, es fundamental que las personas estén listas a seguir adelante incluso después de haber fallado. “No hace falta decir que puede ser frustrante cuando no obtienes los resultados que estás buscando en el laboratorio, pero también podemos aprender de estas experiencias”, asegura Christian Schnatterer. Hemos trabajado en esta área durante más de 85 años. Esto es gracias a Rudolf Kellermann, el fundador de KAMAX, que fue un precursor para su época: empleó métodos de ensayo y laboratorio desde el inicio. Era un adelantado al utilizar métodos científicos en el desarrollo de elementos de fijación y materiales.
después de 720 horas

Para probar un revestimiento recién desarrollado utilizamos varios procedimientos. Las piezas mostradas se sometieron al ensayo de corrosión acelerada (según Volvo STD 423-0014). Esto implica una interacción entre la temperatura (de 35°C a 45°C) y la humedad (del 50 % al 95 %). Además, se lleva a cabo una fase de pulverización dos veces por semana, que dura 45 minutos. Para ello, se utiliza un líquido (mezcla de agua desionizada, sal y ácido sulfúrico) y se hace pasar por tres boquillas del sistema y se pulveriza. En total, estuvieron expuestos a la prueba durante 4 semanas.
KXpress